Late last week the AGLC released a Bulletin (which you can read here) making some amendments to their Liquor Manufacturer Policy. The big news is a relaxing of rules around contract brewing.
The timing of the changes is a bit odd, given we are in a bit of a crisis and fiddling with who can brew where and when seems a bit “not in the moment”, although I will acknowledge contract brewers have been in a bind since the restrictions have been announced.
The way I see it there are two big changes. First, they are allowing contractor breweries (the location where the beer is produced) to act exclusively as contractors and not have to also produce their own product under their brand. I will dub this “The Last Spike Rule”.
Last Spike Brewery, for those who don’t know, is a facility in Calgary that is built to brew beer for other people. They have two brewhouses – 100 BBL and 20 BBL. They are, as far as I know, the only facility of this nature in Canada. Before they opened they hinted that their primary client would be a large, European brewer. Given Last Spike does not share their client information I cannot confirm either which brewery it is or if they are yet brewing at Last Spike.
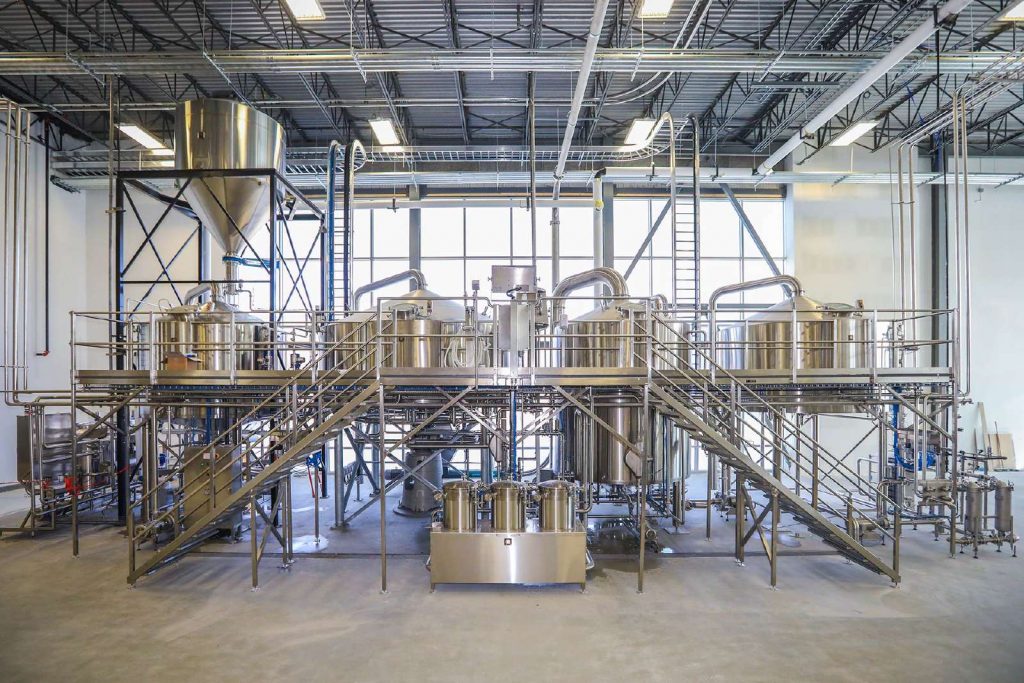
They have also built a thriving business serving Alberta breweries looking for extra capacity and full-time contract breweries without a bricks-and-mortar brewery. The one glitch for them is that, formerly, the rules required them to also produce at least a tiny bit of beer under their own brand to keep their Manufacturer’s License. Again, I have no idea whether they had done this or where they sold it, but I have never seen a can of Last Spike-branded beer.
This policy change frees them of this. From now on they can focus exclusively on their primary business model, brewing beer for other people. This change will be a controversial move, which I will discuss below.
The second change is to loosen the distribution rules for contracted beer. Before it was difficult to distribute beer made at another facility. Basically it had to go through Connect Logistics. No self or direct-distribution was allowed. The new rules allow two new things: the contractor brewery can now distribute the beer on behalf of the contractee (which will benefit Big Rock in particular, who has their own distribution system); and allowing distribution via any AGLC approved warehouse, not just Connect. The latter change has only minor impacts, as there are not too many approved warehouses, but it does create some flexibility.
There were some other minor changes, such as allowing collaboration and contract production as soon as a manufacturing or agency license is issued, adding kombucha to the rules, and loosening rules around the use of pure alcohol and other ingredients in beer production.
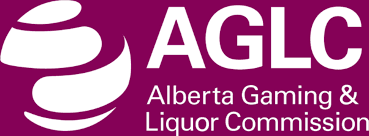
These changes may seem sensible but I am fairly certain they are more controversial than it appears at first blush. There is a tension within the beer industry in Alberta regarding how to handle contract breweries. Proponents of these changes will argue it levels the playing field for contractees and point to the fact the beer still must be produced in an Alberta facility. However, many “bricks and mortar” breweries question equal treatment for contract breweries pointing to the fact, unlike contract brands, they invest hundreds of thousands of dollars in a physical infrastructure, employ staff and actively contribute to the economy, suggesting their is a basis for differential treatment.
Complicating matters further is that there are, basically, three kinds of contract operations. There are “virtual” breweries that have no intention of opening a space of their own. Second, there are “temporary” contractees who are either start-ups contracting while they fundraise/build their own brewery or their existing facility is at capacity and they turn to contracting in the short term to cover demand while upgrading their facility. A third type is quickly emerging. Existing breweries that turn to contracting as a more permanent method to grow, producing a core brand or brands on a larger scale while maintaining small brewhouses for seasonals, specialties, local consumption, etc. Each of these types of contracting elicit different responses from people in the industry it terms of how to treat them. Each requires a different policy solution.
I know the industry players have been grappling with this issue for the last few years. Big questions swirl around regarding eligibility for small manufacturer mark-up rates, access to privileges such as self-distribution, etc. The AGLC bulletin seems to land one of those issues – contract breweries will, in effect, be treated the same as all other Alberta-based producers when it comes to distribution.
For the consumer, knowing who is a bricks-and-mortar brewery and who is a contractee can sometimes be hard to tell (it all depends on how transparent the contractee is). This policy won’t make it any easier to distinguish.
Does it matter who made the beer vs. whose brand name is on it? For some consumers it does, for others not. For the breweries themselves there are potentially big winners and losers here. Which is why I wonder “why now”? Don’t we have enough turmoil in the system?
April 1, 2020 at 12:20 PM
Approved warehouses: every brewery has an aglc approved warehouse for self-distribution so I am guessing that means that if someone is contracting on your system, they can self distribute directly from your warehouse?
April 1, 2020 at 2:24 PM
Hi Kel,
That is true, but I think it means more than that.
There are two separate rules here. One is allowing the contractor to distribute on behalf of the contractee. So any Alberta producer can produce a beer for someone and distribute it.
But then also there is permission to distribute from any approved AGLC warehouse meaning, theoretically (ha! see what I did there?), others not involved in the contract could also be a distributor, if they are on the approved list.